Summary:
Metal and plastic laser marking additives are two types of additives that are used to produce permanent, high-contrast marks on different surfaces. Metal laser marking additives are made of metal oxides or carbides and are applied to metal surfaces, while plastic laser marking additives are made of organic compounds and are added to plastic materials. This article discusses the differences in composition, properties, and applications between metal and plastic laser marking additives. Understanding these differences can help industries choose the best additive for their specific needs and applications.
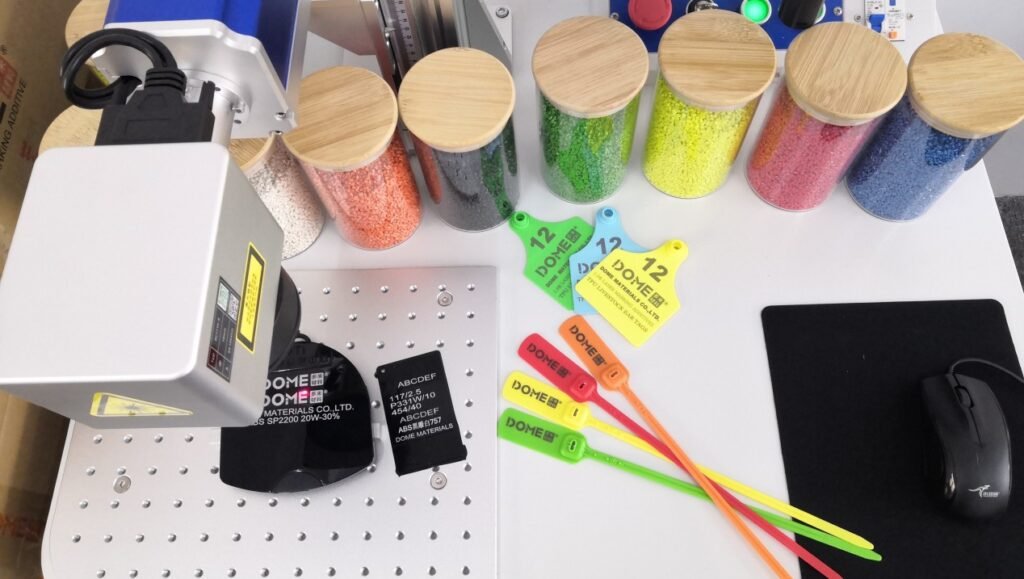
Metal Laser Marking Additives
Metal laser marking additive is a type of material added to the surface of metal components to make them more visible and readable when marked with a laser.
The working principle of metal laser marking additive involves the use of high-powered lasers to etch or engrave the surface of the metal. The additive absorbs the laser energy, causing the metal to change color and create a contrast with the surrounding surface, making it easier to see and read.
To use a metal laser marking additive, it is first applied to the surface of the metal component. The laser beam is then directed at the surface, causing the additive to react and change color, creating a clear and readable mark.
Metal laser marking additive is used in a variety of applications, such as marking serial numbers, barcodes, logos, and other important information on metal components. It is commonly used in industries such as automotive, aerospace, and medical device manufacturing, where traceability and identification of components are crucial for quality control and safety purposes.
Plastic Laser Marking Additives
Plastic laser marking additive is a type of substance that is added to plastic materials to enhance their visibility and legibility when marked using laser technology.
The working principle of plastic laser marking additive involves the addition of a special pigment or compound to the plastic material. This pigment or compound is designed to interact with the laser energy, absorbing some of the energy and converting it into a contrasting color to the base material.
The usage method of plastic laser marking additive involves mixing it with the plastic material during the manufacturing process. The exact amount of additive required depends on the type of plastic and the desired outcome.
The application of plastic laser marking additive is primarily in industries where it is necessary to mark plastic products with permanent and high-contrast text, graphics, or codes. These industries include automotive, aerospace, medical, and consumer electronics manufacturing. The additive can be used with a wide variety of plastics, including polypropylene, polycarbonate, acrylic, and nylon.
Metal laser marking additives and plastic laser marking additives differ in their composition and properties.
Metal laser marking additives are typically made of metal oxides or carbides that have high melting points and are resistant to oxidation and corrosion. They are added to the metal surface to be marked and are activated by the laser beam to create a permanent, high-contrast mark. Metal laser marking additives are commonly used in industries such as automotive, aerospace, and electronics.
Plastic laser marking additives, on the other hand, are typically made of organic compounds such as carbon black or dyes that are specially formulated to absorb the laser energy and produce a permanent mark. They are added to the plastic material itself and are activated by the laser beam to create a high-contrast mark without damaging the material. And Plastic laser marking additives are commonly used in industries such as medical devices, consumer electronics, and packaging.
In summary, metal laser marking additives are used on metal surfaces, while plastic laser marking additives are added to plastic materials. Metal laser marking additives are composed of metal oxides or carbides, while plastic laser marking additives are composed of organic compounds.