Flame retardants are critical plastic additives, enhancing fire safety across electronics, construction, automotive, and aerospace industries. As global regulations tighten and sustainability becomes a priority, the development and application of flame retardants face new challenges. This blog dives into their types, mechanisms, industry applications, selection strategies, and emerging trends.
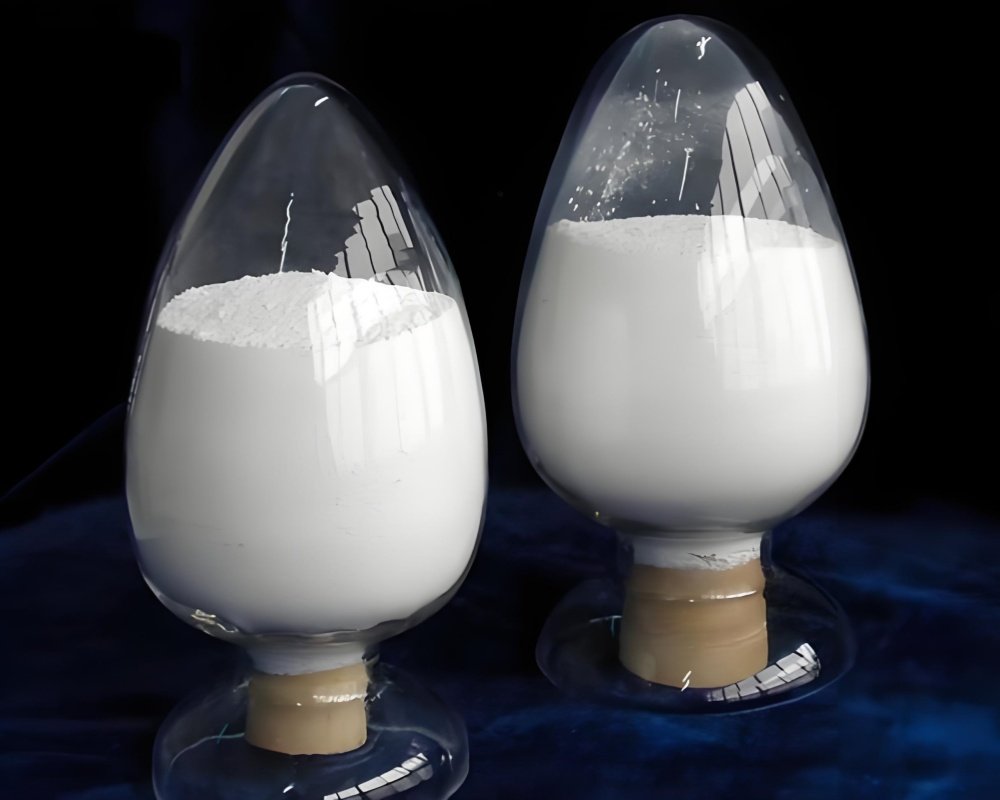
Types of Flame Retardants and Their Mechanisms
Flame retardants are categorized by their chemical composition, each with unique mechanisms to prevent or slow combustion:
- Halogen-Based: Brominated (e.g., decabromodiphenyl ethane) and chlorinated compounds release HBr/HCl at high temperatures, interrupting combustion in the gas phase. Bromine-based options excel in engineering plastics like PC and ABS but face restrictions under EU RoHS due to persistent organic pollutants (POPs).
- Phosphorus-Based: Organic (e.g., triphenyl phosphate) and inorganic (e.g., red phosphorus) variants promote char formation, isolating oxygen (condensed phase). Intumescent systems like ammonium polyphosphate (APP) are eco-friendly and meet UL94 V-0 standards.
- Nitrogen-Based: Melamine derivatives release ammonia to dilute flammable gases, which is ideal for high-temperature materials like PA and PEI when combined with other retardants.
- Inorganic Hydroxides: Aluminum hydroxide (ATH) and magnesium hydroxide (MH) absorb heat and release water vapor. ATH is cost-effective for PP and PE, while MH suits high-temperature processing.
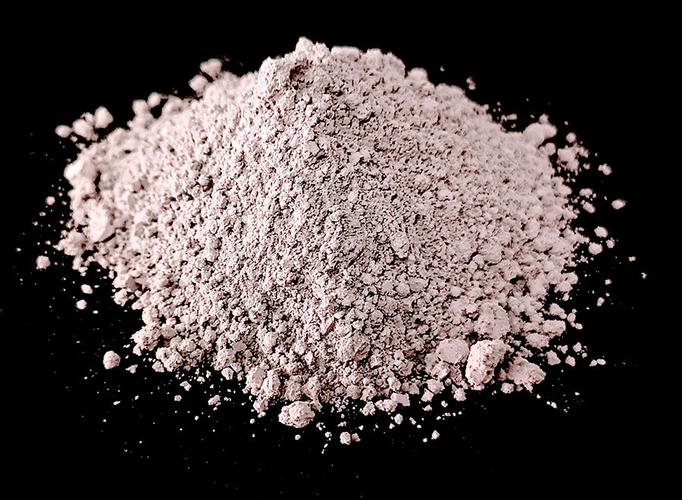
Industry Applications and Selection Criteria
Different industries demand specific flame retardant properties based on material, processing, and safety standards:
- Electronics: Require high heat resistance and low-smoke, halogen-free solutions (e.g., hypophosphites for LCP, brominated polystyrene for compliance with IEC 61249-2-21).
- Construction and Cables: Prioritize cost and extrudability, using ATH/MH blends or brominated polystyrene.
- Automotive: Need low-toxicity options compatible with glass-fiber-reinforced materials, such as piperazine pyrophosphate for GF-PA66.
- Aerospace: Demand extreme temperature resistance and low smoke density, favoring DOPO derivatives and APP.
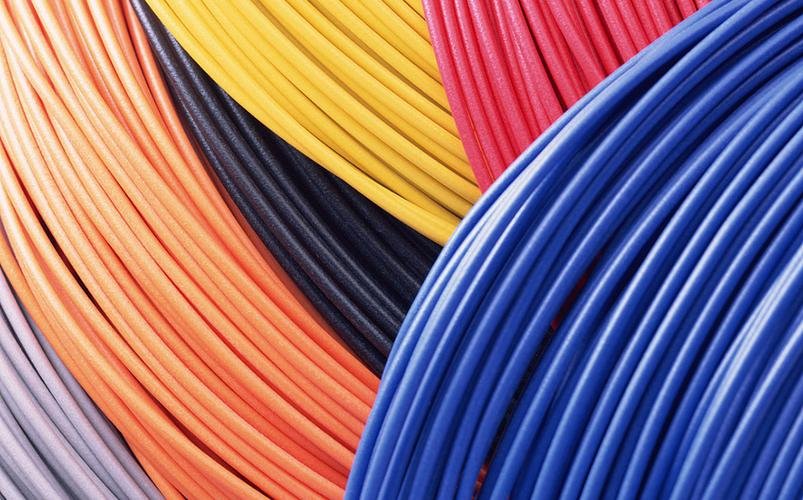
Strategic Selection: Balancing Performance, Cost, and Compliance
Choosing the right flame retardant involves balancing multiple factors:
- Material Compatibility: Match processing temperatures (e.g., phosphate esters for TPE) and ensure compatibility with reinforcements like glass fibers.
- Processing Conditions: High-shear processes require stable retardants like hypophosphites, while MH’s heat absorption aids energy-efficient molding.
- Regulatory Compliance: EU REACH bans certain PBDEs, and UL certifications demand high glow-wire ignition temperatures (GWIT ≥ 850°C). Halogen-free nitrogen-phosphorus systems are gaining traction.
- Cost-Effectiveness: ATH (~$1.5/kg) is economical, while premium options like decabromodiphenyl ethane (~$5/kg) suit high-performance needs.
Future Trends: Green and High-Tech Solutions
The flame retardant industry is evolving toward sustainability and innovation:
- Bio-Based Retardants: Cardanol-derived compounds from cashew nutshells offer eco-friendly, high-stability alternatives.
- Nanocomposites: Graphene and layered silicates enhance char density, reducing retardant loading by up to 30%.
- Smart Materials: Microencapsulated retardants release protection on-demand, optimizing efficiency.
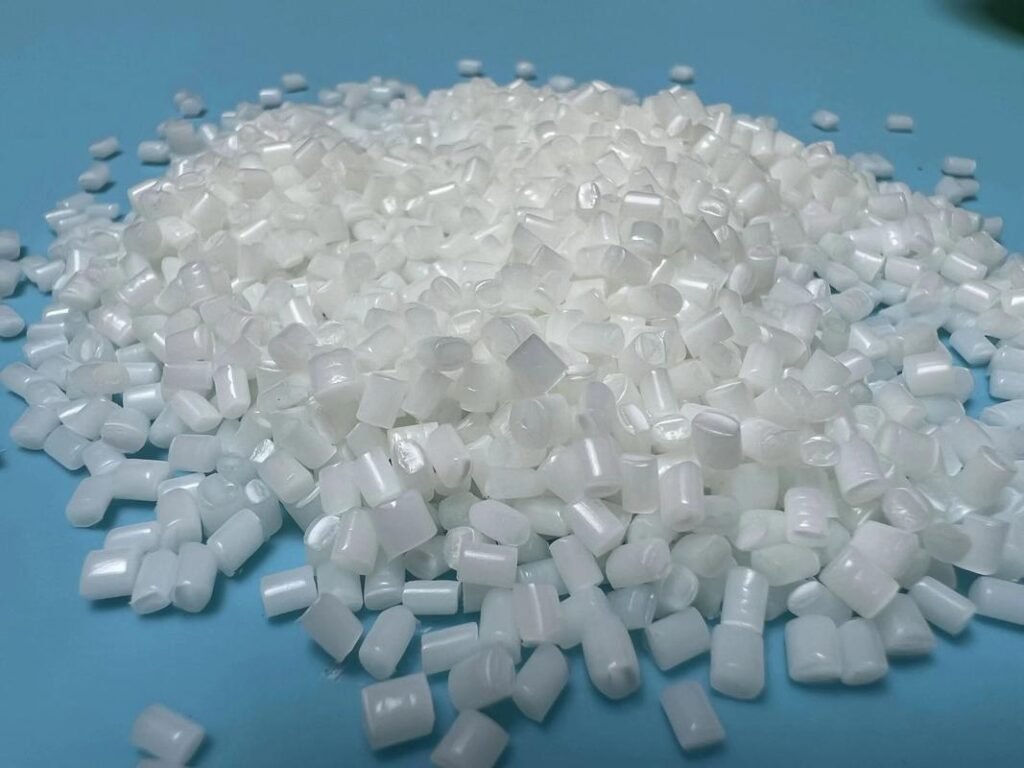
Conclusion
Flame retardants are pivotal for safe, high-performance plastics, but their selection demands a nuanced understanding of chemistry, processing, and regulations. As the industry shifts toward halogen-free, bio-based, and nano-enhanced solutions, staying updated with standards like UL94 and IEC 60695 is crucial. By aligning material science with sustainability, manufacturers can achieve both safety and environmental goals.
References: UL94, IEC 60695, Grand View Research Reports
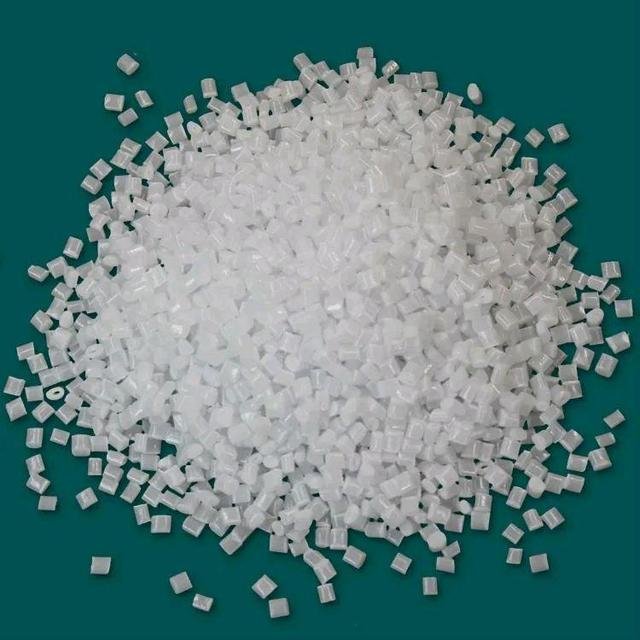