Introduction
In today’s manufacturing landscape, laser technology has emerged as a powerful tool, celebrated for its efficiency and precision. It has become an indispensable force driving the industry toward greater heights. Among its many applications, plastic laser marking stands out for its ability to create fine, permanent markings on plastic materials, offering unparalleled value across various industries. However, achieving optimal results in plastic laser marking is no simple feat. This is where plastic laser marking additives come into play—a “magic key” that unlocks the full potential of this technology. By altering the optical or thermal properties of plastics, these additives enable higher resolution, sharper, and more aesthetically pleasing markings. They are the unsung heroes behind the success of plastic laser marking in modern manufacturing.
In this article, we will explore the principles, functions, applications, and future trends of plastic laser marking additives, uncovering their pivotal role in advancing this innovative technology.
What Are Plastic Laser Marking Additives?
Plastic laser marking additives are specialized chemical substances added to plastic materials to enhance their laser marking performance. Laser marking relies on high-energy laser beams to create permanent markings by inducing localized melting, vaporization, or chemical changes on the material’s surface. However, natural plastics often exhibit low laser energy absorption, resulting in subpar marking quality, such as uneven patterns or thermal damage. Plastic laser marking additives address these challenges by modifying the optical or thermal properties of plastics.
Key functions of these additives include:
- Enhancing Light Absorption: By improving the plastic’s ability to absorb specific laser wavelengths, additives act as “energy amplifiers,” enabling sharper, more detailed, and higher-resolution markings.
- Improving Thermal Stability: Additives help plastics withstand the heat generated during laser marking, reducing the risk of thermal damage and ensuring smooth, high-quality results.
- Increasing Marking Contrast: By altering the color or reflectivity of the marked area, additives create striking contrasts, making patterns and text more visible and easier to read.
In essence, plastic laser marking additives are crucial for achieving clear, precise, and durable markings, laying the foundation for the widespread adoption of this technology in modern manufacturing.
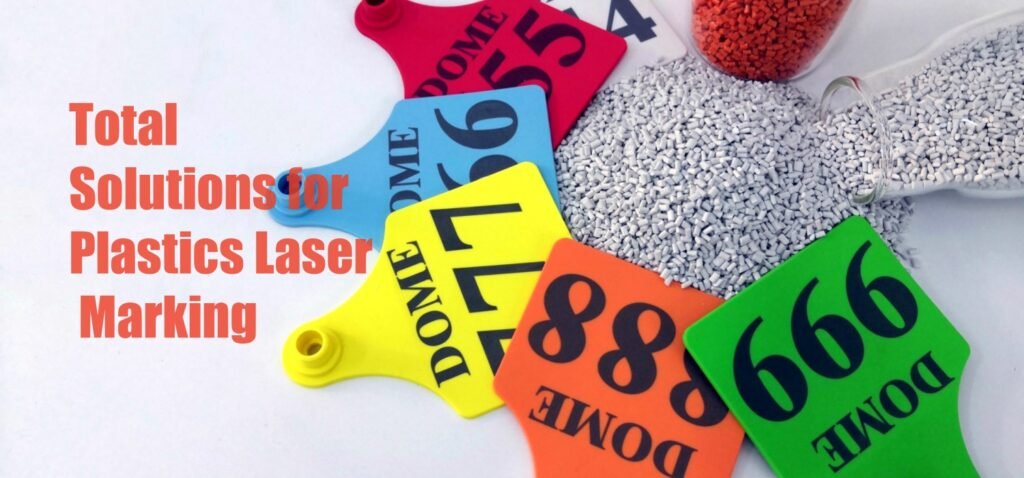
How Plastic Laser Marking Additives Work
Enhancing Light Absorption
Laser beams operate at specific wavelengths, and natural plastics often have low absorption rates for these wavelengths, limiting marking effectiveness. Additives address this by enhancing the plastic’s light absorption properties, effectively turning the material into a more efficient “energy receptor.”
For instance, in applications requiring high-resolution markings, such as serial numbers on electronic devices, additives enable plastics to absorb laser energy more effectively. This results in crisp, detailed markings with enhanced precision, meeting the stringent requirements of industries like electronics.
Improving Thermal Stability
During the marking process, the laser generates heat, which can cause localized overheating, deformation, or damage to plastics with low thermal stability. Certain additives mitigate these issues by optimizing the material’s heat conduction and resistance properties.
For example, in automotive interiors, where durability and aesthetics are critical, additives help prevent thermal damage during laser marking, ensuring that components like dashboard panels and seat headrests retain their structural integrity and visual appeal
Increasing Marking Contrast
Additives can chemically or physically alter the marked area’s color or reflectivity, creating sharp contrasts between marked and unmarked regions. For example, when marking white plastic packaging, additives can darken the marked area to produce highly visible patterns or text, enhancing readability and recognition.
This feature is especially valuable in industries like packaging, where clear and durable markings—such as expiration dates or product information—are essential for consumer safety and regulatory compliance.
Applications of Plastic Laser Marking Additives
Electronics Manufacturing
In the electronics industry, plastic laser marking additives play a crucial role in achieving precise and durable markings on device components such as smartphone casings, laptop covers, and tablet shells. These markings often include brand logos, serial numbers, and QR codes, which are vital for product identification, traceability, and after-sales service.
Without additives, natural plastics may produce markings that are faint, uneven, or prone to wear over time. Additives enhance the absorption of laser energy, ensuring that markings are sharp, high-resolution, and resistant to wear, even under prolonged use or friction.
Automotive Industry
The automotive sector demands high-quality laser markings on interior components, such as dashboards, door panels, and seat headrests. These markings must be durable enough to withstand temperature fluctuations, friction, and UV exposure.
Plastic laser marking additives improve the thermal stability of materials, preventing deformation or discoloration during the marking process. Additionally, they enhance contrast, ensuring that logos, patterns, or functional markings are visually striking and seamlessly integrated into the vehicle’s interior design.
Medical Devices
In the medical field, precision and permanence are critical for markings on plastic devices such as syringes, infusion tubes, and diagnostic equipment. These markings provide essential information, including specifications, expiry dates, and usage instructions, which must remain legible throughout the product’s lifecycle.
Laser marking additives ensure that these markings are durable and resistant to sterilization processes, such as autoclaving while maintaining the safety and biocompatibility of the plastic material.
Packaging and Labeling
Plastic laser marking is increasingly popular in the packaging industry for creating clear and permanent labels on products ranging from food and beverages to consumer goods. Additives enhance the contrast and durability of these markings, ensuring that information such as production dates and batch numbers remains legible throughout the supply chain.
For example, in transparent plastic packaging, additives can darken marked areas to create highly visible text or patterns, improving readability and enhancing the overall aesthetic appeal of the product.
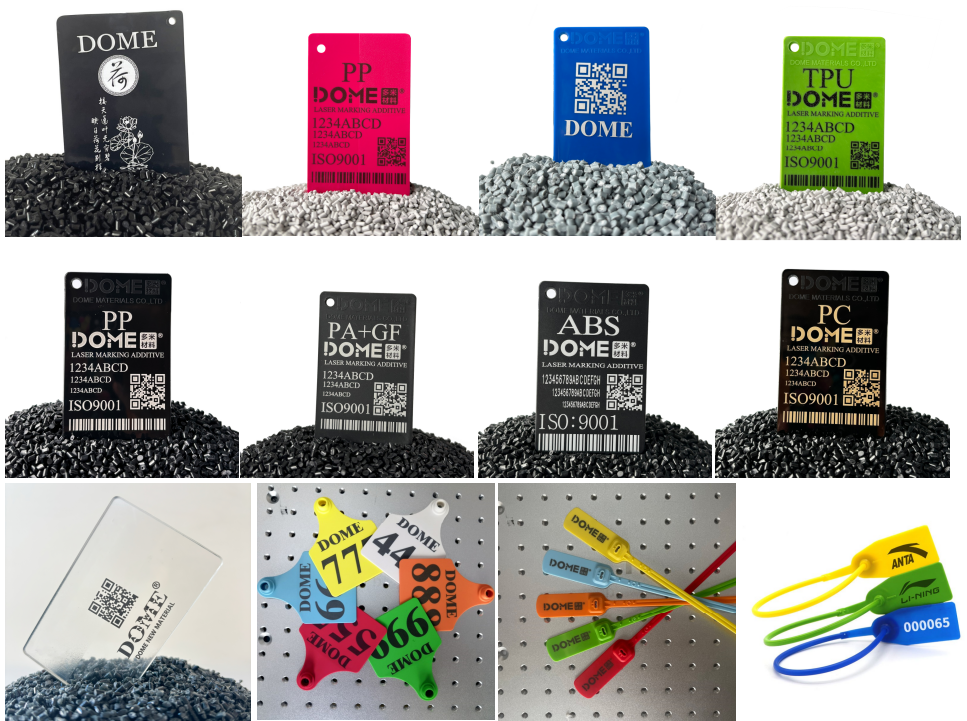
Future Trends in Plastic Laser Marking Additives
Sustainability and Eco-Friendliness
As environmental regulations tighten, the development of eco-friendly plastic laser marking additives is becoming a priority. Traditional additives may pose environmental risks during production or disposal, but next-generation additives are being designed with sustainability in mind.
These eco-friendly additives use biodegradable or non-toxic materials and cleaner manufacturing processes, reducing their environmental impact without compromising performance. They enable manufacturers to achieve high-quality markings while aligning with global sustainability goals.
Multifunctionality
The future of plastic laser marking additives lies in multifunctionality. Beyond enhancing marking performance, additives are being developed to impart additional properties to plastic materials, such as:
- Antibacterial Properties: Particularly valuable in medical applications, where preventing bacterial growth is critical.
- Flame Retardancy: Essential for industries like automotive and electronics, where fire safety is a top priority.
These multifunctional additives will expand the scope of laser marking technology, enabling plastic materials to meet diverse application requirements.
Smart Integration with Intelligent Manufacturing
The integration of plastic laser marking additives with smart manufacturing systems opens up exciting possibilities. Intelligent systems can dynamically adjust additive concentrations and distributions based on real-time marking requirements, ensuring optimal performance for different applications.
For instance, in mass customization scenarios, additives can be precisely tailored to meet the specific needs of each product, enhancing efficiency and reducing waste. This smart approach aligns with the broader trend of Industry 4.0, driving greater automation and precision in manufacturing processes.
Conclusion
Plastic laser marking additives have become an indispensable innovation in modern manufacturing. By enhancing light absorption, improving thermal stability, and increasing marking contrast, these additives address the limitations of natural plastics, enabling high-resolution, durable, and aesthetically pleasing laser markings. Their applications span diverse industries, from electronics and automotive to medical devices and packaging, underscoring their versatility and value.
Looking ahead, developing eco-friendly, multifunctional, and smart additives promises to revolutionize the field, paving the way for sustainable, efficient, and intelligent manufacturing. As the manufacturing industry evolves, plastic laser marking additives will play a pivotal role in shaping its future.