Summary:
Plastic injection molding technology is the most important production process in the plastics industry. We utilize plastic injection molded products in every aspect of our lives and employ various other procedures to enhance the value of the final product. Laser marking on plastic injection molded parts is one of them.
There are several advantages to using laser marking in the plastic molding manufacturing business. Various industries widely utilize plastic laser marking additives in various raw materials and modified plastic compounds. These additives aid in the efficient and uniform absorption of laser energy by plastic products, resulting in improved clarity, speed, and contrast in engraving performance. Currently, plastic laser marking additives have been extensively applied in industries, such as plastic seals, plastic lead seals, safety seals, animal ear tags, plastic cables, plastic pipes, electronics, lighting, automobiles, household appliances, and more.
Laser marking systems bring multiple advantages to the industries that use them, as well as injection molding operations. This article will introduce what laser marking additives are, how they work, some of the main advantages of using a laser marking system, the main factors affecting laser marking results, application tips, precautions, etc.
What are Plastic Laser Marking Additives?
Laser marking additives, also known as laser colorant, laser powder, laser marking powder, laser marking masterbatch, etc. Laser marking additives are suitable for laser coding. It can greatly improve the clarity of laser marks on plastic, nylon, and other materials to obtain higher-definition marks without affecting the color and performance of plastic products.
Plastic does not absorb laser light. Therefore, laser marking additives are added to plastics to make them more sensitive to laser energy. A wider range of plastics can be marked using laser technology.
Laser marking additives have very strong laser sensitivity and significant color change effects. The main function of laser marking additives is to absorb laser energy, convert laser beams into heat energy, and produce heating, carbonization, evaporation, and chemical effects on plastics. Reaction, laser marking additives have different marking effects on plastic laser marking with different chemical properties. Laser marking can be roughly divided into three types according to the effect:
Mark dark color on a light-colored plastic substrate
Under the action of high temperature generated by laser irradiation, foaming will occur inside most plastic collectives, and laser marking is generally gray. This laser marking method mainly uses a laser to generate high temperatures inside the plastic, resulting in collective oxidation, thermal degradation and even burning. The chemical reaction causes local charring changes. The purpose of these marking additives is to promote high-temperature charring of the plastic substrate and improve laser marking edge definition.

Mark light color on a dark plastic substrate
The laser marking process is a thermal reaction process. After the dark plastic substrate is irradiated by the laser, it burns or vaporizes, and foaming occurs inside. These bubbles are surrounded by the plastic substrate and then irradiated with suitable laser energy. A mixed phase with higher refractive index results in a light-colored mark. Such additives are generally black substances such as carbon black or pigments, which can form a strong color contrast after being added, thereby producing a good laser marking effect.
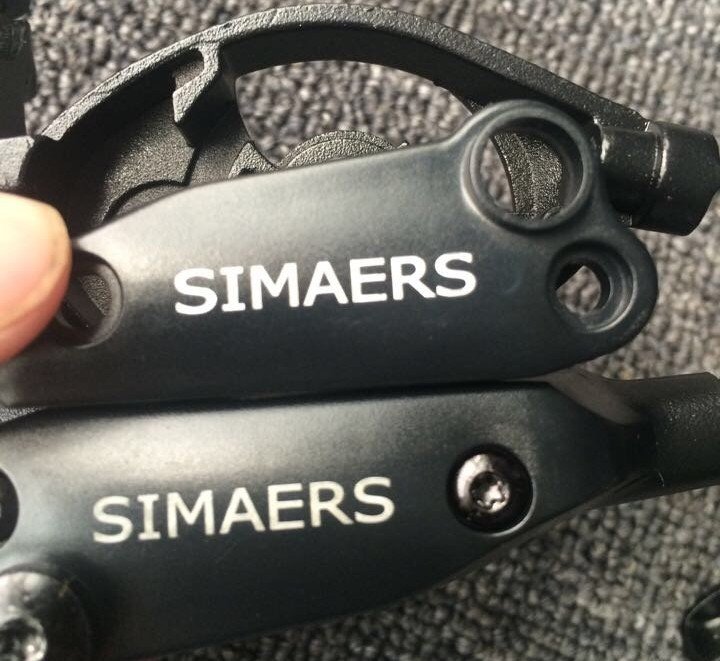
Color marking on plastic substrates
Certain plastic substrates are physically difficult to laser mark in color. Chemical modification of such plastics is commonly used starting from the modification of plastic substrates, adding laser marking colorants or pigments, and using laser energy to degrade or react with the colorants. As a result, the laser marking produces a color change, presenting a laser color marking.
The Principle of Laser Marking
Laser machines emit high-energy pulsed laser beams. When the laser beam acts on the material to be marked, the light energy is converted into heat energy under the action of the laser marking additive, causing the surface of the material to melt, foam, change color or even gasify, thereby forming a graphic.
Carbonization
After being irradiated by laser, the laser additives will generate heat so that the surrounding resin will be charred and carbonized, leaving black marks on the workpiece, and this method is generally suitable for light-colored substrates. Generally common in the technology of “white plastic marking black”.
Foaming
The additive generates heat to achieve the degree of degradation of the resin and generates heat to form a large number of fine bubbles on the substrate, which can produce light-colored or white marking effects, which are suitable for dark-colored and black substrates. Generally common in the technology of “black plastic marking white”.
Ablation
Using a high-energy laser to completely vaporize the resin to create a concave texture on the substrate. Generally used in laser direct structuring (LDS).
Additives self-discoloration
After being excited by the laser, the additive undergoes a chemical change, making the color of the additive darker. This method is suitable for light-colored substrates. Generally used in the technology of “light-colored plastic marking black”.
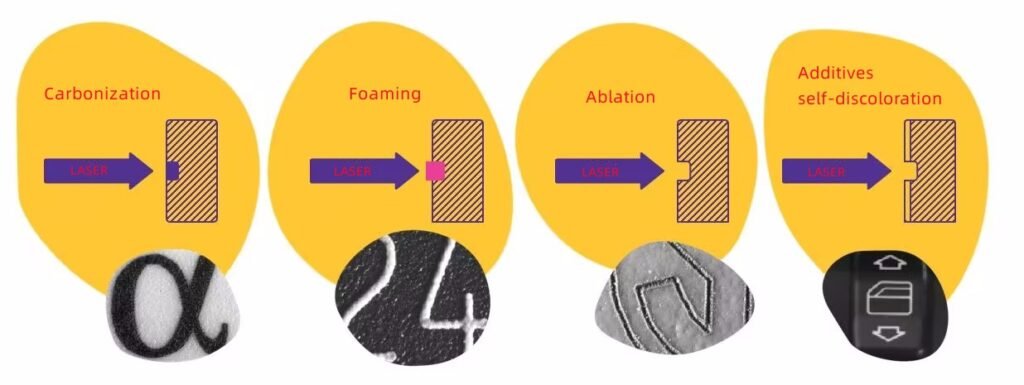
Why do I need laser marking additives?
With the advancement of technology, there are various marking technologies available for plastic products, such as printing, spraying, and laser marking. Laser marking offers several advantages, including flexible marking, durability, reliability, non-contact operation, and no need for consumables. It is an economical and environmentally friendly marking method widely used in the plastic industry.
However, most polymers are somewhat “transparent” to the beam emitted by conventional commercial laser machines. As a result, the laser beam passes through the plastic without being absorbed, leading to less visible laser marking. To address this issue, DOME plastic laser marking additives provide enhanced and safer solutions for plastic laser marking applications.
Laser marking additives, also known as laser absorbing additives or laser radiation engraving additives, enable lasers to produce readable marks on thermoplastics and certain polymer resin applications.
They have been extensively used in various product forms, ensuring stable quality and compliance with regulations. Applications include polymer film packaging, bottle caps, equipment requiring tracking, tracing, and sterilization in hospitals and laboratories, animal ear tags, submarine cables, light switch covers, cosmetic packaging materials, automotive interior buttons, and door handles, dashboards, ABS keypads for business machines, HDPE, LDPE, PET, and PVC rigid containers and container covers, nylon and PBT automotive and non-automotive electrical connectors, hood components such as fuse boxes and gas caps, anti-counterfeiting labels, container locks, stationery, home appliance shells, and more.
These additives provide uniform marking color and exhibit strong heat and light resistance. The choice of laser marking additives and equipment may vary across industries and factories, resulting in different levels of laser marking effects.
By incorporating laser-sensitive additives into plastic, high-contrast marks that are easily visible to people can be created. These high-contrast markings are useful for identification purposes, creating warnings, and displaying other important information that needs to be highly visible.
Furthermore, by carefully selecting the appropriate laser marking additives, it is possible to create marks that are resistant to fading, sun damage, and other environmental factors. This makes them ideal for marking applications that require prolonged exposure to the elements.
To choose the right laser marking additive for your specific application, it is recommended to collaborate with a professional supplier. With over ten years of experience in the development and production of plastic laser marking additives, DOME can assist you in understanding the available options and making informed decisions.
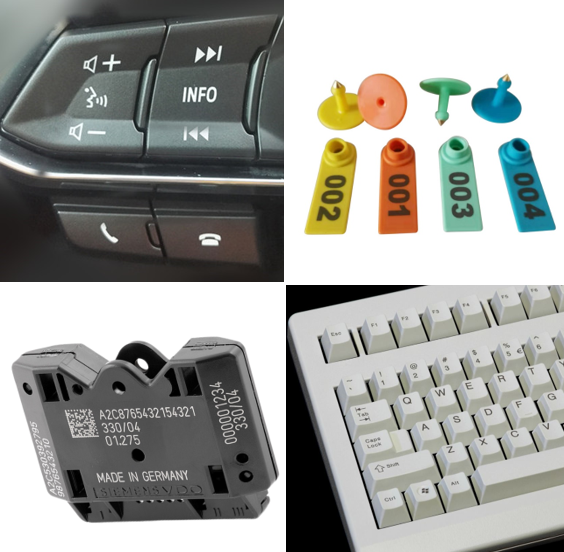
How to choose, laser Marking powder or laser marking masterbatch?
There are 2 types of plastic laser marking aids with different physical forms: powder and granular.
The material form of the laser absorbing additive: the left is granular, and the right is powder:
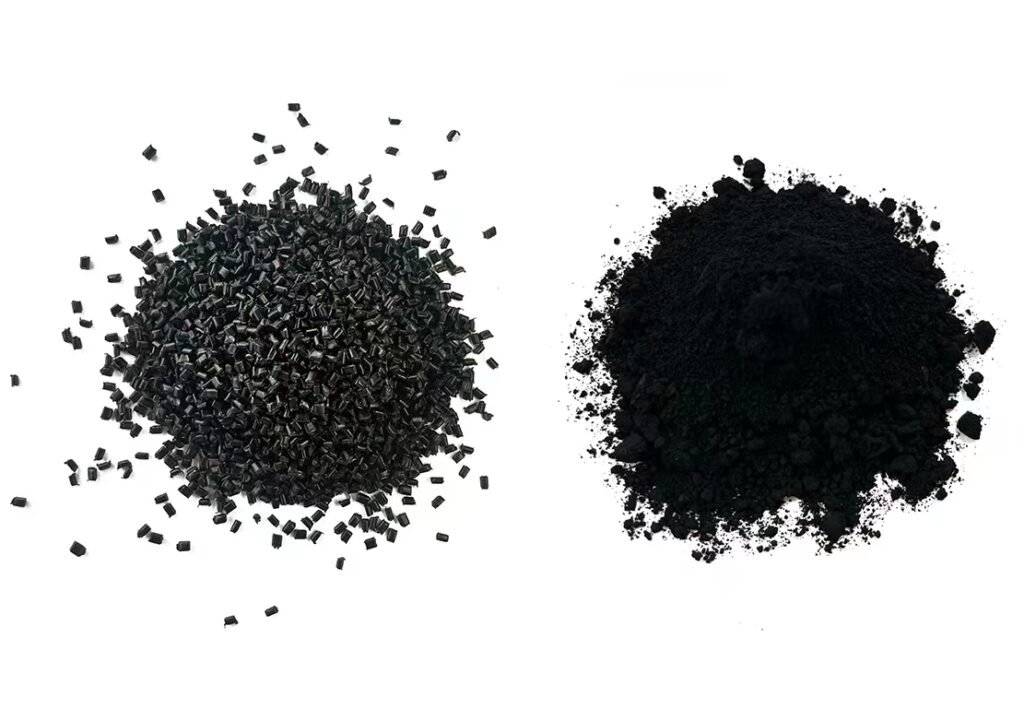
When deciding between laser marking powder and laser marking masterbatch, it is important to consider their different physical forms and material compositions. Laser marking masterbatch is a granular additive that typically contains a carrier plastic like PE or TPU. This form of additive is advantageous because it can be easily dispersed during the injection molding process, resulting in a more uniform marking effect. However, the downside is that a higher amount of laser marking masterbatch, typically 2%-5%, needs to be added.
On the other hand, laser marking powder requires a lower addition amount, usually 0.3%-0.5%, making it more cost-effective compared to radium engraving masterbatches. However, it is important to note that laser marking powder is relatively heavier and tends to sink to the bottom if directly injected. To ensure a uniform dispersion, the powder needs to be granulated before use.
In summary, laser marking masterbatch is preferred for its ease of dispersion during injection molding but requires a higher addition amount. Laser marking powder is more cost-effective but needs to be granulated to achieve uniform dispersion.
Which types of plastics can be marked with laser marking additives?
No matter the type of industry you represent, the marking and identification of parts are critical to its operations. Laser marking technology is one of the most versatile innovations in the field of engraving. The laser marking aid can help the laser to leave a clear and durable laser mark on the plastic surface, and the mark is clear, durable, and will not disappear due to mechanical, chemical, and physical factors.
Laser marking aids can be applied to a variety of plastic resins including polycarbonate, acrylonitrile butadiene styrene (ABS), polyethylene (including low-density polyethylene (LDPE) and high-density polyethylene (HDPE)), and Polyethylene terephthalate (PET). In general, laser marking additives provide a means of creating high-contrast marks on plastics that are otherwise difficult to mark. It is suitable for most general-purpose plastics and some engineering plastics such as PP, PA, PBT, PVC, TPU, PS, TPE, TPV, TPR, PET, PC, POM, PEI, UP, ABE, nylon, epoxy resin, and other materials, Can also be used for plastic alloys such as; PC+ABS and other materials.
Wide application of Laser marking masterbatch/powder in plastic thermal conductive materials
Compared with traditional aluminum materials, plastic heat-conducting materials have the advantages of being lightweight, more environmentally friendly, and safer production process, improved design freedom, more convenient processing and higher efficiency, and simplified start-up system. In the future, plastic heat-conducting materials will gradually replace Aluminum and become one of the best heat-conducting materials.
The main application fields of plastic heat-conducting materials such as PPS, PA6/PA66, LCP, TPE, PC, PP, PPA, and PEEK, etc. include LED lighting, automobiles, heating/cooling/refrigeration, etc.; Components made of thermally conductive materials will inevitably be marked with some logos, graphics, fonts and other manufacturer information and product parameter instructions.
However, due to the limitations of the base material of the plastic heat-conducting material, problems such as blurred and unclear marking images and low recognition degrees may occur when laser marking is used. After adding laser marking masterbatch/laser marking powder, the effect will be significantly improved, which solves the above problems well, and basically has no effect on the thermal conductivity and other physical properties of the substrate itself.
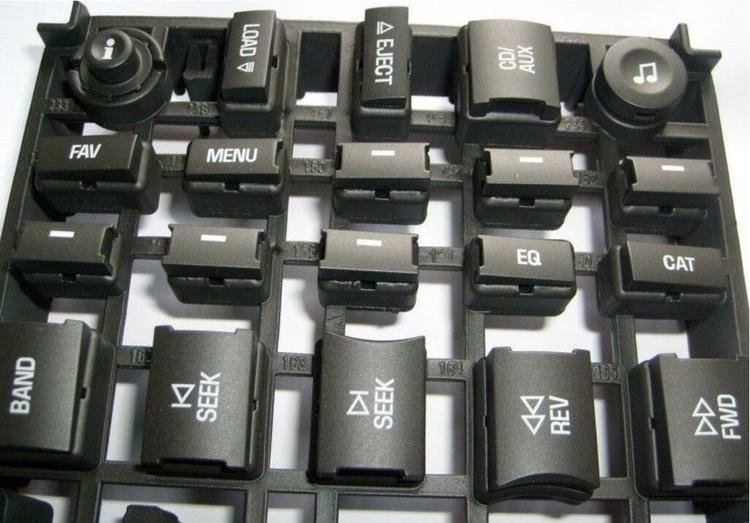
Application of plastic marking aids on thermoplastic elastomer materials such as TPE/TPU/TPR/TPV
For plastics with different chemical properties, there are different varieties of light laser marking on dark plastic and dark laser marking on light plastic.
Nowadays, more and more thermoplastic elastomer TPU / TPE / TPR / TPV wires, shoe materials, pipes, etc. require laser marking, because compared with traditional ink printing, laser marking is more economical, environmentally friendly, highly anti-counterfeiting, and marking accuracy High traceability and other advantages. Adding laser marking powder to thermoplastic elastomer products can significantly improve the effect of laser marking, the font is clearer and more beautiful, the recognition is higher, the stability of laser engraving, and the marking speed is significantly improved.
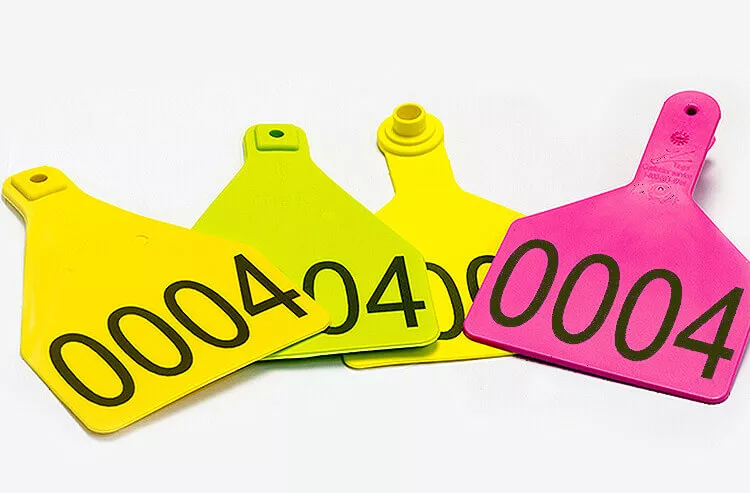
How to choose the right laser marking additive for your application?
There are a few things to consider when choosing the right laser marking additive for your application. First, you need to consider the type of plastic you want to mark. Second, you need to think about the specific results you’re looking for. Finally, you need to consider the cost of the additive and its compatibility with your laser system.
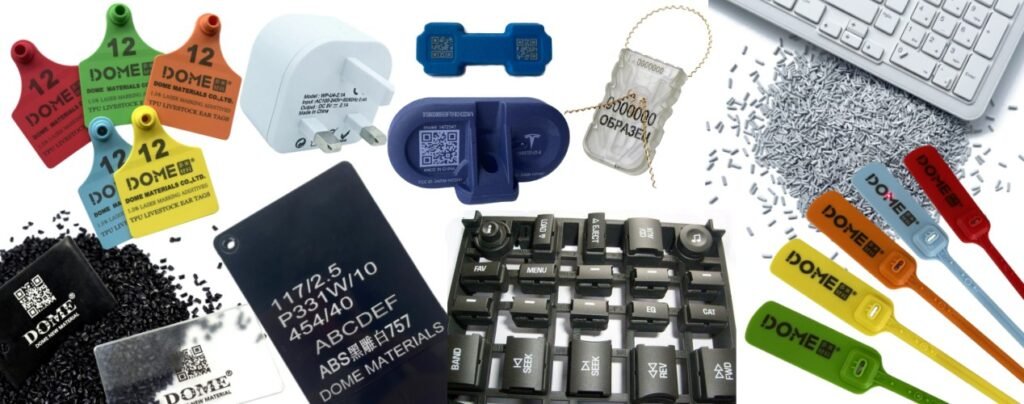
What are the main factors that affect the effect of plastic laser marking?
There are many influencing factors that need to be considered, mainly including raw materials, laser marking additives, the amount of laser marking additives, laser marking machine selection, laser marking parameter settings, etc., which are affected by many aspects.
Amount of additives for plastic laser marking
DOME laser marking additive (laser marking powder), the recommended addition amount is 0.3%-0.5% under normal circumstances, that is, add about 3-5 grams of plastic radium engraving powder to one kilogram of raw materials. The recommended addition amount of laser marking masterbatch is 1 %-3%, that is, adding about 10-30 grams of plastic radium engraving masterbatch to one kilogram of raw materials. There are modifications such as flame retardant and fiber addition, and the amount of addition should be increased appropriately. Of course, the actual amount added depends on its own cost and the standard requirements for the effect of laser marking.
Baking material for plastic laser engraving additives
Laser marking additives usually cannot be baked. The raw materials must be dried before adding our laser marking additives. Otherwise, the materials will only dissolve together and the raw materials will be scrapped. Laser marking additives specially developed for plastics with high melting points can be baked together.
Raw materials
When using laser engraving additives for black plastic laser marking characters of other colors, the effect is the best if new virgin raw materials of natural color are used; if it is mixed-color recycled materials, the effect of laser marking is not as good as that of new materials; do not use black materials directly. That will seriously affect the effect of laser marking.
Selection of Laser Marking Machine Types
At present, there are two types of laser marking machines commonly used in the market. The first type is ultraviolet laser marking machines, which are characterized by stable speed and no consumables. However, it also has obvious disadvantages. It is only effective for some plastic formulations, and it is difficult to meet the labeling needs of all products through material modification. Equipment maintenance costs are relatively high, and consumables such as lenses need to be replaced regularly.
The other type is an infrared laser marking machine, which is roughly divided into three types according to different laser devices: end pump (Nd: YAG), optical fiber (Fiber), and CO2 (gas). Among them, the infrared fiber laser marking machine is a typical representative, which has the characteristics of fast speed, good stability, and strong versatility. It can meet the laser marking needs of most materials through the compounding of materials and laser-absorbing additives.
Black Plastic Marking White/Black Plastic Marking Gold
We require raw materials for laser engraving to be natural or transparent. Do not add other black colors, black color masterbatch, black color paste, etc. during the marking process. After adding our laser marking additives, the material will be dyed black, and then directly laser Just marks it. Because adding too many black colors will affect the absorption of the laser by the laser marking additive, thus affecting the effect of black engraving white/gold. If you feel that the blackness is not enough in the later stage, you can deepen the blackness by adding organic oil-based black, which is made from red, yellow, and blue toner. Do not use black seeds, carbon black, and other pigment masterbatches.
Laser technical parameters
Several parameters need to be carefully adjusted during the laser marking process to achieve the correct level of precision and contrast. The balance between power, frequency, and scan speed to generate the correct heat on plastic surfaces requires a high level of expertise. Often, many people do not adjust the parameters of the laser machine but only use a fixed parameter for laser engraving. If they feel that the engraving is not good, they will change it from the added amount, which will only increase the cost blindly.
Will plastic laser engraving additives affect product color?
All laser marking additives have an influence on the color of the plastic itself, and most of them have relatively little influence, which depends on the plastic itself. Usually, the solution is just to adjust by adding toner.
Can DOME laser marking additives achieve satisfactory light-color markings on colored plastic surfaces?
Generally, infrared laser machines are used for laser marking on plastic materials such as yellow, green, purple, or blue. It is difficult to obtain high-contrast laser marks, especially light-colored marks. When using traditional laser marking additives, even by increasing the amount of laser marking additives or adjusting the parameters of marking speed, frequency, or energy, it is difficult to achieve satisfactory light-color marking on the surface of colored plastics. How to solve it?
DOME’s color plastic marking white laser marking additive mainly absorbs laser light energy by itself, converts light energy into heat energy, and then transfers it to the surrounding polymer, causing the polymer to foam and form a white mark. This reaction mechanism makes it possible to white mark on the surface of colored plastics, can achieve higher contrast laser marking with the lower additive amount and faster speed, and is suitable for most polymers and various colors.
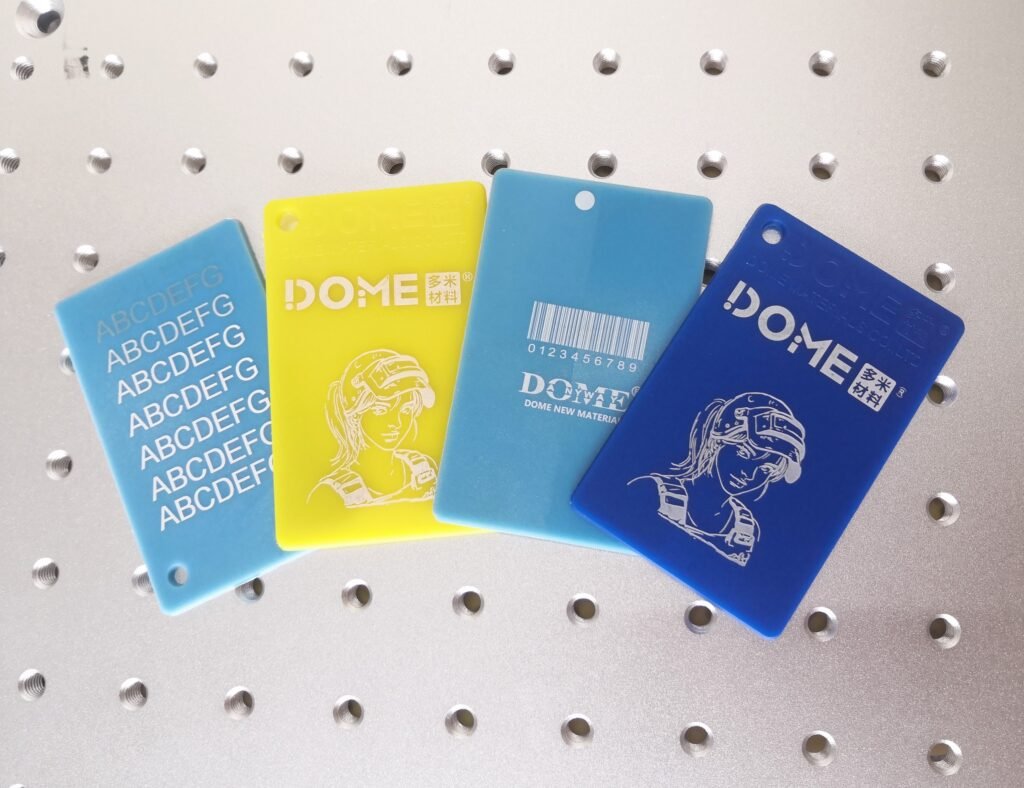
What are the advantages of plastic laser marking?
Laser marking is considered one of the best solutions for permanent marking on thermoplastics. Compared with traditional printing or spraying, it has the following advantages:
- Environmentally friendly
After the plastic injection molding is completed, it is directly marked on the laser machine. The marking process does not require the participation of solvents and other organic substances, which is environmentally friendly.
- Flexibility
Patterns, fonts, numbers, characters, etc. can be freely edited and replaced in the laser machine editing window according to the needs of the designer.
- Convenience
There are no plastic polarity concerns, electrostatic treatments, flame-treated surface pre-treatments, or “last-hand polishing” of plastic parts. cut costs.
- Efficiency
Compared with traditional engraving methods, the production speed is faster. High-speed automated marking is possible, and embossed and concave designs are difficult to engrave using conventional techniques. However, the ability of the laser beam to reach all areas makes it extremely easy. This means the process is both time-saving and cost-effective.
- Precision
Laser marking is highly accurate, provides clear-resolution graphics, and can produce high-resolution micro-marks, and the accuracy of the results makes it a very reliable technology for important parts manufacturing and marking.
- Permanent
Markings will not fade or wear out over time, bringing effective value to product traceability.
- Sustainability
The laser marking solution introduces no pollutants and facilitates plastic recycling. In addition, the marking process uses a focused laser beam, laser scanning, non-direct contact, and less wear and tear on tooling and equipment.
When should laser marking additives be used?
Laser marking additives are used in a variety of applications including identification marks, barcodes, and logos. They can also be used for decorative purposes. In general, laser marking additives are most commonly used when creating high-contrast marks on plastic surfaces is important.
If you’re looking for a way to create high-contrast marks on plastics, laser marking additives could be the right solution for you. When making your decision, be sure to consider the type of plastic, how you want to mark, the colors you need to mark, and the cost of additives. Moreover, if you have any questions, please be sure to consult our DOME professional laser engraving auxiliary hormone personnel. We can help you choose the right additive for your application and ensure you get the best results.
How to use laser marking additives?
- Dry the raw materials, and then add laser engraving additives.
First of all, the laser marking additive does not need to be baked. If the laser engraving additive is added and baked together with the raw materials, the temperature is too high and the baking time is too long. It is recommended to dry the raw materials first, and then add our laser engraving additives, then the laser engraving can be injected normally.
- Stir the raw materials and laser marking additives evenly, and then directly inject or pump pellets.
There are two common ones in the plastic process, which are first pumping pellets and then injection molding and direct injection molding. Usually, if it is a direct injection molding process, it is recommended to use masterbatch laser marking additives, because the powder will sink to the bottom of the powder is heavy and unevenly dispersed during injection molding. If it is a granulation process, the effect of using laser marking powder and laser marking masterbatch is very good.
- After injection molding the finished product, it can be marked directly with a laser machine.
In the process of laser marking, it is necessary to continuously change the parameters of the laser to engrave, so as to achieve the best laser engraving effect. Often many people do not adjust the parameters of the laser machine, but only change the amount added, which will only increase the cost blindly.
What factors should be considered when using plastic laser marking additives?
- Remember to dry the plastic raw materials without moisture;
- The effect of laser marking depends on various factors. In addition to laser marking additives, the additives in plastics, colorants, the quality of the laser machine, and the parameter settings of the laser machine also have very critical factors. Customers may have to make Various tests can find the best laser marking solution.
- Glass fiber or glass beads will not have a great impact on the marking effect.
- In the process of marking white on black plastic, it is recommended that the total amount of carbon black added should not exceed 1.5% of the resin. Excessive carbon black will reduce the laser marking performance.
- PP colored with carbon black can produce a black plastic marking white effect, but for industrial production, the continuous marking of finished products is very important, adding an appropriate amount of laser marking additives can make the finished product have a higher speed and stable marking effect, and the use of laser engraving materials will have better clarity.
- Adding flame retardants will greatly reduce the marking effect and clarity, so the proportion of laser marking additives should be significantly increased in the formula.
- In general, the process of marking black on white substrates relies on the reaction of plastics to carbonization and blackening at high temperatures. Therefore, it is recommended to use low power and low Q frequency settings on the laser engraving machine. On the other hand, marking white on black substrates is achieved by decomposing the material at high temperatures. This decomposition process generates numerous small bubbles that protrude from the plastic’s surface, resulting in a lighter color. As a result, light colors can be effectively marked. We will suggest using higher power and Q frequency when marking to make it have a better whitening effect.
- Storage conditions: Laser marking (laser engraving) powder is dust-free granule or powder, clean, simple, and safe, and it is not a dangerous good; please store it in a dry and ventilated place; waterproof and moisture-proof; avoid exposure to sunlight; unused parts please Store airtight; use within 24 months.

Conclusion
No matter the type of industry you represent, the marking and identification of parts are critical to its operations.
No matter what type of additive you use or what type of machine you need, it’s important to do your research and find the right additive for your needs.
Plastic laser marking is an art. The process is delicate and requires careful tuning of several parameters to achieve the correct level of precision and contrast. The balance between power, frequency, and scan speed to generate the correct heat on plastic surfaces requires a high level of expertise.
If you have any questions about choosing the right plastic laser marking aid for your needs, please feel free to contact us. We are always happy to help!